Digitalization and data analysis empower us to deliver increasingly efficient, customized maintenance for your packaging machinery and manufacturing packages.
In recent years, maintaining optimal efficiency in your packaging machine has become crucial for ensuring consistent and reliable performance over time.
At Galdi, including our branch Galdi Inc, our advancements in technical support are closely aligned with the ongoing digitalization process and the utilization of precise data regarding the status and efficiency of each filling machine. This progress has enabled us to introduce new services that provide real-time remote assistance and pave the way for tailored maintenance solutions.
Ultimately, this approach will enhance our ability to evaluate component lifespans accurately, significantly reduce downtime and emergency maintenance, and eliminate unnecessary waste and costs.
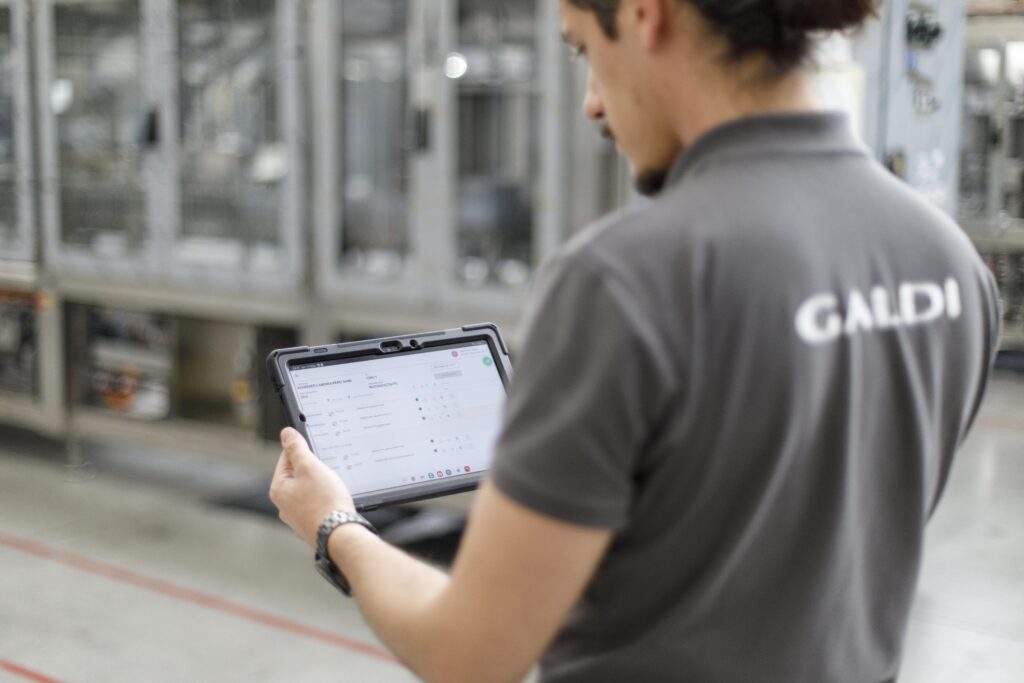
Advancing Galdi Maintenance Services with a Tailored Manufacturing Package
Effective maintenance is crucial for ensuring that your packaging machinery and manufacturing package operate at peak performance over time.
Drawing on our extensive industry expertise, we have developed a Preventive Maintenance Plan (PMP) that offers detailed guidelines for scheduling interventions and replacements based on production hours. Furthermore, we provide customized maintenance contracts, enabling our customers to tailor the level of after-sales support they desire, from comprehensive maintenance packages to scheduled on-site visits from Galdi experts.
Digitalization has also allowed us to introduce exclusive digital services, such as MaSH, Galdi’s advanced monitoring system, and real-time remote assistance.
Advancing Towards Predictive Maintenance
Our long-term vision is to implement personalized maintenance plans (PMP) that are tailored to the actual wear and tear of components within your manufacturing package. To achieve this, we are developing advanced software that is currently in the final stages of development. Our engineers are utilizing this innovative tool to analyze data from a variety of sources, including:
- Specific “Meters” Linked to Critical Components provide real-time data on the performance and condition of essential machine parts.
- Technicians’ Activities on the Machines: in the future, we plan to enable customers to report interventions, further enriching the data pool actively.
- Meter Data Collection accurately measures the usage of individual components, such as the number of doses, caps, or cartons packed, allowing for precise tracking of wear.
Our system seamlessly integrates all meter and technician data with regular updates, empowering the algorithm to plan interventions based on the machine’s actual operating conditions.
For instance, if your PMP indicates that a specific part should be replaced after 1,000 hours of operation, the software can dynamically adjust the timing of the intervention based on real usage patterns. Additionally, it can identify and suggest other maintenance tasks that could be performed during the same service visit, optimizing efficiency.
The result is a truly personalized maintenance approach for the entire packaging line, delivering a multitude of benefits, including:
- Optimal Utilization of Component Lifespan: ensuring that each part is used to its fullest potential before replacement.
- Reduction in Total Cost of Ownership (TCO): we help lower overall costs by minimizing unnecessary replacements and maximizing efficiency.
- Improved Spare Parts Management: streamlined processes for tracking and managing spare parts inventory.
- Decrease in Critical Events: reducing the frequency of urgent repairs or replacements, leading to smoother operations.
- Enhanced Production Stability: sustaining high efficiency over time, ensuring that your manufacturing package operates at peak performance.
Embracing the Future: The Path to Predictive Maintenance
Data will play a crucial role in the future of maintenance. The insights gathered from individual machines are already proving invaluable for several key areas:
- Optimizing Technician Efficiency: by tracking all machine activities, we can enhance the productivity of our technicians.
- Enhancing System and Maintenance Efficiency: valuable insights can be extracted to improve both system performance and maintenance operations, such as identifying components that require replacement within a specific timeframe.
- Refining Design Accuracy: operational data and technician feedback help designers enhance the technical precision of our equipment.
As we gather more data and integrate Machine Learning, predictive maintenance represents the next frontier in our approach. We are making significant strides towards this goal by:
- Optimizing Sensors and Developing Predictive Models: this phase has already been completed.
- Analyzing Data for System Refinement: this process is currently underway.
- Implementing Machine Intelligence Systems: our ultimate objective is to establish adaptive and predictive maintenance capabilities.
With predictive maintenance, intelligent and reliable packaging machines will be equipped to:
- Continuously Self-Monitor: ensuring optimal performance at all times.
- Recommend Timely Interventions and Replacements: facilitating proactive maintenance and minimizing downtime.
Galdi Inc. is committed to delivering innovative solutions that ensure consistent efficiency levels, maximum cost optimization, and the elimination of unforeseen events.
By focusing on advanced technologies and personalized maintenance plans, we aim to enhance the performance of your manufacturing package and provide intelligent food packaging machines that truly represent the future of the industry.
Our dedication to continuous improvement and customer satisfaction positions us as a leader in the packaging sector, ready to meet the evolving needs of our clients while driving operational excellence.